Permanent magnet rotor e1655961736623.jpeg.
Rotor position information is necessary for the control of a permanent magnet synchronous motor (PMSM) and position sensorless control is the trend for its low cost, high reliability and space-saving.
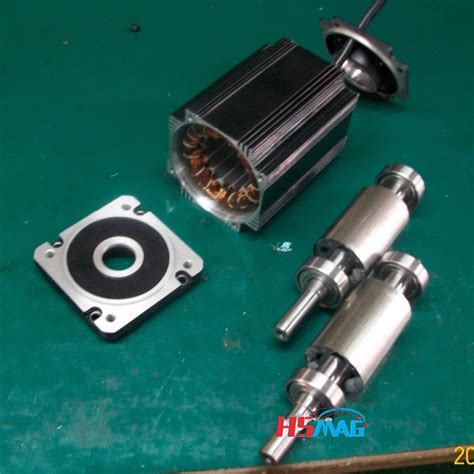
An interior permanent magnet synchronous motor (IPMSM) with ‘VV—’ shape rotor topology structure is proposed. The established two-dimensional (2D) parameterized finite element analysis (FEA) models are used to analyze and compare the output average torque, torque density, air-gap flux density and back electromotive force …This paper compares two flux-switching machines, namely, one stator permanent magnet flux-switching machine and one rotor permanent magnet flux …A magnet is a material or object that produces a magnetic field. This magnetic field is invisible but is responsible for the most notable property of a magnet: a force that pulls on other ferromagnetic materials, such as iron, steel, nickel, cobalt, etc. and attracts or repels other magnets. A permanent magnet is an object made from a material ... Axial flux permanent magnet synchronous motors (AFPMSMs) have been widely used in wind-power generation, electric vehicles, aircraft, and other renewable-energy applications owing to their high power density, operating efficiency, and integrability. To facilitate comprehensive research on AFPMSM, this article reviews the developments in …
In this paper, an improved rotor position observer with sliding mode control strategy of permanent magnet synchronous motor was studied. A MPF was designed instead of LPF to reduce the chattering in the traditional SMO back EMF and eliminate the system phase delay.Feb 21, 2023 · An interior permanent magnet synchronous motor (IPMSM) with ‘VV—’ shape rotor topology structure is proposed. The established two-dimensional (2D) parameterized finite element analysis (FEA) models are used to analyze and compare the output average torque, torque density, air-gap flux density and back electromotive force (EMF) of the IPMSM with ‘V’ shape, ‘V—’ shape, ‘VV ...
Lee et al. (5, 6) proposed a rotor supported by the permanent/electromagnetic magnetic bearing (PEMB) to operate well under the control of four simple analog PD controllers. In this study, the design considerations of the PEMBs and the method for analyzing the complete rotor-bearing system are presented. Also, a …
Coaxial counter-rotating propellers have been widely applied in ships and helicopters for improving the propulsion efficiency and offsetting system reactive torques. Lately, the counter-rotating concept has been introduced into the wind turbine design. Distributed wind power generation systems often require a novel approach in generator …2.2 External rotor permanent magnet motor rotor air gap magnetic field When the motor is running at no load, the air gap magnetic field is provided by the permanent magnet alone. The generated magnetic field rotates together with the rotor and the rotational speed is synchronous speed.This paper is focused on the optimal design, simulation, and experimental testing of a counter-rotating double-rotor axial flux permanent magnet synchronous …Today’s automotive industry has focused its studies on electric vehicles (EVs) or hybrid electric vehicles (HEVs) rather than gasoline-powered vehicles. For this reason, more investment has been made in electric motors with high efficiency, high torque density, and high-power factor to be used in both EVs and HEVs. In this study, an outer-rotor …
The windings of coreless axial flux permanent-magnet machine (CAFPM) are exposed to the rotor magnetic field, where each back electromotive force (EMF) harmonic is induced not only by several ...
Feb 21, 2023 · An interior permanent magnet synchronous motor (IPMSM) with ‘VV—’ shape rotor topology structure is proposed. The established two-dimensional (2D) parameterized finite element analysis (FEA) models are used to analyze and compare the output average torque, torque density, air-gap flux density and back electromotive force (EMF) of the IPMSM with ‘V’ shape, ‘V—’ shape, ‘VV ...
Jul 1, 2017 · Unbalanced magnetic force (UMF) is one of the most important issues in permanent magnet (PM) machines with rotating asymmetric winding configurations, where the UMF is intrinsic [1, 2]. When these machines are perfectly manufactured, they show good electromagnetic performances such as high efficiency, high torque density, low torque ripple and ... 1 Introduction. Over the past decades, the development of the power train with simple structure and high reliability has always been a hot topic in academic research [].Traditional power train with DC motor with double rotor has the shortcomings of poor efficiency and excessive noise [2, 3].Compared with DC motor, permanent magnet …Jun 23, 2022 · The rotor overtemperature caused by losses is one of the important issues for the high-speed electrical machine. This paper focuses on the rotor loss analysis and CFD-thermal coupling evaluation for 105 kW, 36,000 r/min HSPMSM. Three types of sleeve materials as carbon-fiber, Titanium alloy, and stainless steel are introduced in this paper, researching the effects of sleeve conductivity ... A new technique for high performance and robust speed control of permanent magnet synchronous motor (PMSM) using a mixed non-linear H∞ and Sliding Mode Control (SMC) is applied.Understanding permanent magnet motors. A permanent magnet (PM) motor is an ac motor that uses magnets imbedded into or …The windings of coreless axial flux permanent-magnet machine (CAFPM) are exposed to the rotor magnetic field, where each back electromotive force (EMF) harmonic is induced not only by several ...
In order to address these issues, a 2-DOF surface permanent magnet spherical motor with a new mechanical design for the movement of the rotor with a large tilt angle of ±45° was designed, simulated, produced and tested in this paper. The motor consisted of a 4-pole permanent magnet rotor and a 3-block stator with 18 coils.A flux-reversal permanent-magnet motor with the magnetic-differential application is presented in this paper. The motor adopts radial-field double-rotor structure. By artfully integrating a set of windings into the motor, the motor is able to realize differential without the bulky differential gear, making the propulsion system in electric vehicles more …Eddy current losses in magnets are a major consideration in the rotor design of permanent magnet synchronous motors (PMSMs). Stator design choices and the use of modern inverters with high switching frequency introduce harmonics that can contribute to significant losses in the magnets, causing the rotor to heat up. In typical …reluctance, thus creating a magnetic pull to rotate the rotor. PM motors are driven by the interaction of the magnetic field generated by the permanent magnets and the rotating magnetic field generated by the stator winding. The characteristics of these high-speed motors are shown in Table1[61]. As can be seen from Table1, the high-speed …In this study, an analytical model is established to efficiently compute the magnetic field and unbalanced magnetic pull (UMP) in axial-flux permanent-magnet motors (AFPMMs). The effects of stator …
An ironless rotor structure wastes permanent magnet material, since the magnetic circuit closes through air in the rotor side. Therefore, a thin steel rim, to which the magnets are attached, is employed (Fig. 9.1) The rim can be either a laminated structure, in which case the eddy current losses of the rotor remainExternal rotors of “outrunner” type. Rotors with additional bandage (Polyglas, Kevlar, carbon) Rotors with protecting sleeve. Contact us. Jan Kratochvil ml. +420 607 570 823 …
2.1 Design of Rotor Eccentric Arc and Performance Analysis. This paper takes a permanent-magnet rotor as an example. Figure 1 shows 1/8 models of a rotor without an eccentric arc design, a rotor core designed with a conventional eccentric arc, and a rotor core designed with the improved eccentric arc. The permanent magnets of the …Nov 11, 2021 · According to the location of permanent magnet on the rotor, the permanent magnet synchronous motor rotor mainly has two different structures: surface-mounted and buried. Due to the strength limitation of silicon steel sheets, the application of buried rotor in the high-speed field is relatively smaller than surface-mounted rotor. 1 Introduction. Over the past decades, the development of the power train with simple structure and high reliability has always been a hot topic in academic research [].Traditional power train with DC motor with double rotor has the shortcomings of poor efficiency and excessive noise [2, 3].Compared with DC motor, permanent magnet …The research is devoted to the investigation of NdFeB permanent magnet (PM) based synchronous generators with non-overlapping concentrated windings. The rotor of such …The advantages of choosing Sintex® magnetic rotors are as follows: Patented solutions. Complete solutions. 100% sealed enclosure – can run as wet runner. Corrosion-resistant materials. High efficiency / low energy loss. Maintenance-free. Long service life. …Harmonic Distortion is very low at <2% giving superior waveform, meaning that our low rpm permanent magnet generators help you guarantee the safe operation of modern sensitive electronic equipment. When using our low rpm pmg generators, power density is increased using inverter technology, where the traditional excitation winding systems are ... A stationary magnetic field is produced across the rotor by poles on the stator. These poles may be encircled by field coils carrying direct current, or they may contain permanent magnets. The rotor or armature consists …Mar 20, 2021 · Reluctance is a function of rotor position in a variable reluctance motor. Sequential switching (Figure below) of the stator phases moves the rotor from one position to the next. The mangetic flux seeks the path of least reluctance, the magnetic analog of electric resistance. This is an over simplified rotor and waveforms to illustrate operation. Sep 2, 2020 · In the PMSG that has not been the CT reduction technique, the rotor permanent magnets (PMs) have an increasing effect on the CT since each PM has the same relative position with reference to the stator slots . The CT in each PM is in the same phase as the others, so, the harmonic component of each is added together then, CT has become higher.
rotor. For the rotor, the back iron δ BI and the magnet thicknesses δ PM have to be determined, which will also determine the inner rotor radius. In order to achieve high torque, the rotor should be chosen narrow (leading to a large radius of the magnetic gap, which is the lever arm of the motor). However, the permanent magnets have to provide a
In this paper, an optimal design procedure which includes multi-physics analysis to design the multi-phase external rotor PMa-SynRMs is presented. In specific, a five-phase external rotor PMa-SynRM with neodymium based magnets has been proposed as a solution to produce higher power density compared to the conventional internal rotor PMa-SynRMs ...
Summary. PM (Permanent Magnet) Type: uses permanent magnets, moderate torque, low to mid-speed. VR (Variable Reluctance) Type: toothed rotor/stator, low torque, mid to high speed. Hybrid Type: combines permanent magnets and teeth, good combination of torque and speed.Arnold produces high performance permanent magnet motor components and sub-assemblies for aerospace and defense, industrial, automotive, and motorsport applications, such as: KERS — Kinetic Energy Recovery …In order to get rid of the bulky and lossy differential gears and to enhance the system robustness, the magnetic differential (MagD) system is proposed after the mechanical differential (MechD) and electronic differential (ElecD) systems. The MagD system is mainly composed of the double-rotor (DR) stator-permanent-magnet (PM) …Synchronous motor. Miniature synchronous motor used in analog clocks. The rotor is made of permanent magnet. Small synchronous motor with integral stepdown gear from a microwave oven. A synchronous electric motor is an AC electric motor in which, at steady state, [1] the rotation of the shaft is synchronized with the frequency of the supply ... The rated power and speed of the permanent magnet grinding electric spindle are 7.5Kw and 950r/min, respectively.The main parameters of the PMGES are as follows, the rotor mass is m = 5.66 kg; the rotor radius is R = 0.072 mm; the axial length of the air gap is L = 0.178 mm, nominal air gap length is δ 0 = 3 × 10 −3 m, air permeability …Permanent magnet traction motor has the advantages of high efficiency, high power density, high torque density and quick dynamic response, which has been widely used in the traction field of electric vehicle. The high-performance control of permanent magnet traction motor depends on accurate rotor position information, which is usually …In this paper, an optimal design procedure which includes multi-physics analysis to design the multi-phase external rotor PMa-SynRMs is presented. In specific, a five-phase external rotor PMa-SynRM with neodymium based magnets has been proposed as a solution to produce higher power density compared to the conventional internal rotor PMa-SynRMs ...Oct 14, 2002 · The most important magnet layouts in rotors of hybrid permanent-magnet synchronous machines (PMSM) for electric vehicles are compared in a variety of characteristics. The effect of different rotor designs on the vehicle performance and energy consumption is evaluated for a small battery electric vehicle (BEV) for different drive cycles. A surface-mounted permanent magnet synchronous motor (SPMSM) is an electric motor with a simple magnetic circuit design, fast responsiveness, linear torque–current characteristics, speed–voltage characteristics, and constant operating speed. SPMSMs use only magnetic torque; however, interior PMSMs (IPMSMs) have high …
The equivalent magnetic circuit (EMC) is employed both to design the mechanical parameters of the rotor while considering nonlinear magnetic saturation effect and to analyze the magnetic characteristics of the air-gap of the motor. This paper considers the design and performance evaluation of interior permanent magnet …where Φ is the magnet flux crossing the air gap, R is the total reluctance through the flux paths and θ is the rotor angle. It is clear that if the reluctance R does not vary as the rotor rotates, then the cogging torque T cog is zero. From this point of view, the cogging torque can be improved by changing the V-shape rotor structure variables …(PMSM) into the market. Permanent magnet synchronous machines have been applied to servo drives for a long time already, and nowadays, there are quite large permanent magnet synchronous machines also in industrial use. In wind mill generators, the development has currently been in the direction of permanent magnet machines. Instagram:https://instagram. apartments for rent in tacoma wa under dollar600api schemai 94 expired but i 797 is validul6fbengal kittens for sale dollar300z40integrated Jan 31, 2017 · Understanding permanent magnet motors. A permanent magnet (PM) motor is an ac motor that uses magnets imbedded into or attached to the surface of the motor’s rotor. This article provides an elementary understanding behind the terminology, concepts, theory, and physics behind PM motors. nirvana hoodie urban May 30, 2023 · Currently, research is being carried out on the performance improvement of permanent-magnet-synchronous motors (PMSM) used in air conditioning and blowing systems for marine, as well as structural research, regarding their high-speed operation. Surface-mounted permanent magnet (SPM) motors used in marine propulsion and air-conditioning systems have the advantages of easy rotor manufacturing ... Dec 15, 2023 · Interior permanent magnet (IPM) motors in traction applications often employ discrete rotor skewing constructions to reduce torsional excitations and back-EMF harmonics. Although skewing is very effective in reducing cogging torque, the impact on torque ripple is not well understood and can vary significantly over the operating envelope of a motor. Skewing also leads to the creation of a non ...